
Replace the 90-degree bracket with a custom bracket that matches the downward angle of the rear leg.
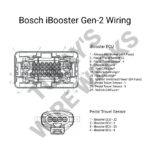
The issue with that approach is that the tubes welded to the firewall would need to extend an inch or so past the body which, as shown above, extends well into the engine compartment and, at least in my case, would cause them to interfere with the supercharger during engine removal. I considered welding a section of tube to a plate mounted to the firewall and using interlocking tube couplers to enable a section of the leg to be easily removed. Given that I must remove the rear hoop legs to remove the engine and removing the body requires removing the doors, headliner, windshield (which I risk cracking) and removing and then reinstalling all of the sealing around the foot box, side pods and firewall, this is an untenable situation. With the body on, it would be easy to get the rod end installed, but the misalignment washers and grade 8 washer - NFW.
#Ibooster gen 2 install#
I struggle to install the rod ends and washers when the body is removed, I’m standing in the center of the cockpit and have prefect access to everything. HOWEVER, as can be seen in the picture below, the body significantly overhands the rod ends and it’s somewhere between a nightmare and impossible to install things when the body is on. Last thing you want is foreign-object damage when you start the engine.Ĭonceptually this isn’t problem because the rear legs aren’t removed very often once the car is finished and you want everything tight. Sometimes one hits the floor and rolls to God knows where and you can spend a lot of time looking for it on the floor or on the front engine dress. It’s difficult to get the washers and misalignment washers in place, let alone properly aligned, and if they fall you need to find them all because one might be in the supercharger, accessory or dry sump belt. In fact, the body of one of my rod ends actually binds on the bracket. The issue is that the standard RCR suspension bracket is utilized which requires a high-misalignment rod end, two aluminum misalignment washers and a grade-8 washer to be crammed at an awkward angle. It takes me longer to install those two bolts, than it does to install the other 14 bolts combined. However, it’s a royal pain in the ass to install the rod ends that connect the rear legs to the top of the rear hoop. I’ve removed/installed the cage many times and it’s a pretty quick and easy process. My takeaway for titanium is that in addition to material the tooling and machining costs are noticeably higher. With tools, my general philosophy is “buy once, cry once” and while McMaster charges a premium, I get it one day and I don’t need to worry about quality. Taps designed for titanium have a different coating and spiral flutes, so I ordered a $47.17 tap from McMaster. NFW was I going to finish the hole without breaking the tap.Īpparently, titanium’s low modulus of elasticity makes it “springy,” so the workpiece tends to close in on the tap causing galling and tearing of the threads which also increases the torque on the tap. After replacing it with one specifically designed for titanium, I quickly determined that my tap was a no go. A piece of 6” long by 1/2” OD Grade 5 titanium rod cost me $33.85 and part way through drilling my first hole I wrecked a high-quality, made-in-the-USA drill bit. With aluminum, stainless steel or 4130, I’d have the material laying around and the machining would be straight forward. I fabricated threaded 1/4”-20 bosses from 1/2” Grade 5 titanium rod. I had the corners precut so I only needed to sand the straight edge with the tabs.
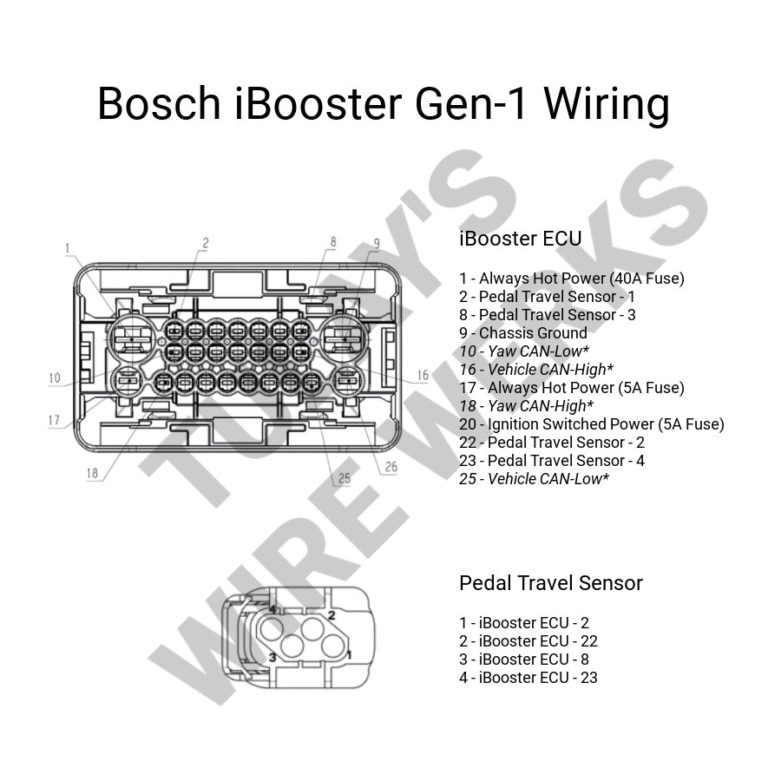
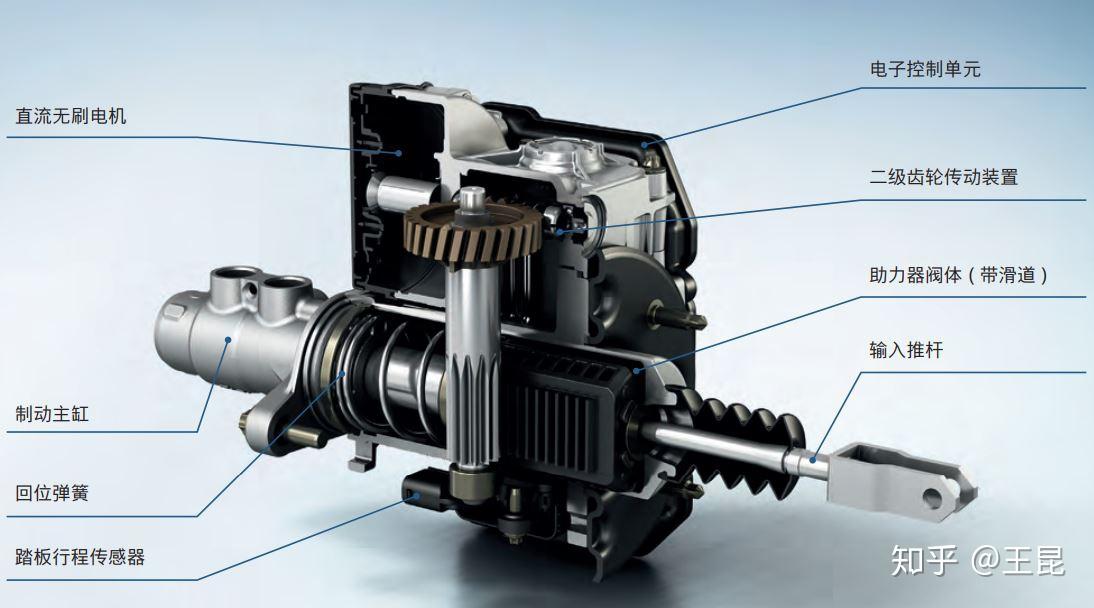
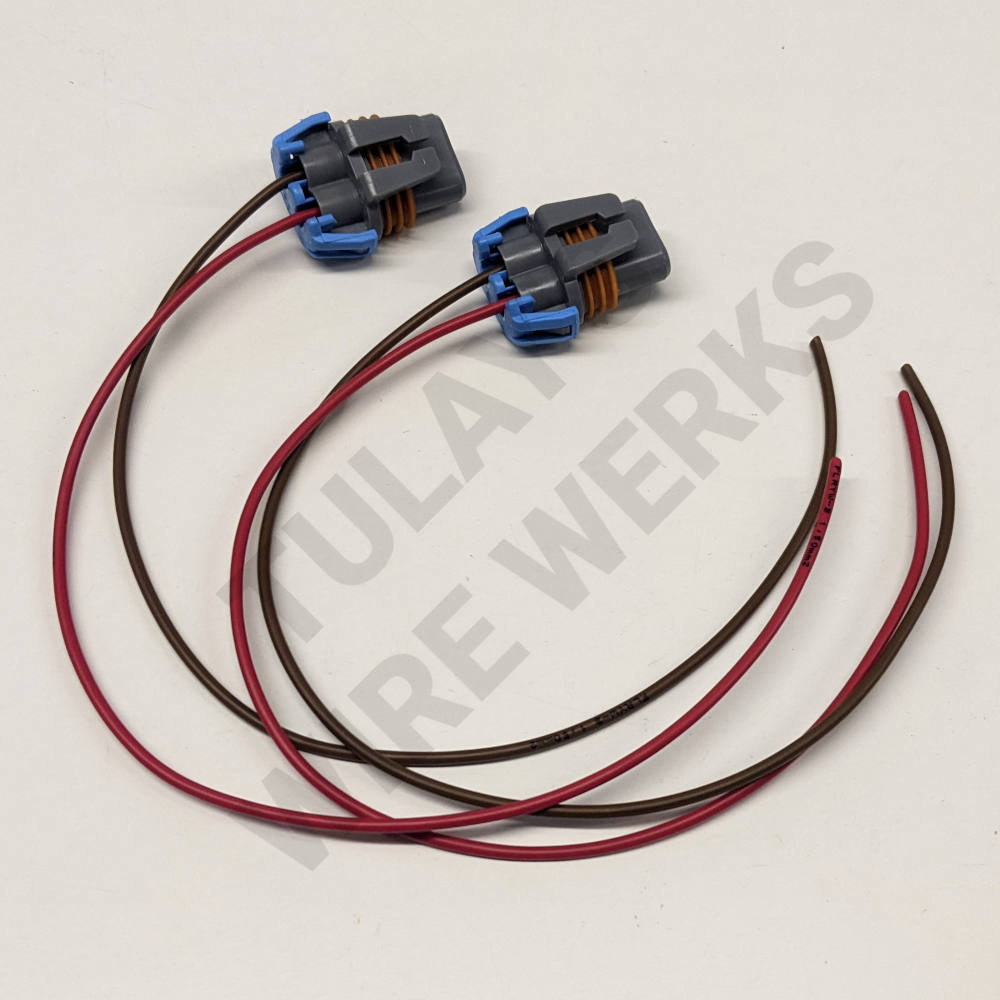
They also recommend that each tab is spaced out by 1x the material thickness which seems a seems a bit excessive. I took a closer look at SCS’s guidelines and it recommends that the tab width is 50% the material thickness which seems right (mine were twice that wide). The tabs required more effort than I anticipated to remove. After the part arrived, I cut the extension off and sanded the edge smooth. The extension is attached via small tabs to facilitate removal. This requires that edge to be parallel to the bend line - which it wasn’t.Īs can be seen in the picture below, the solution was to extend the sloped sides to create an edge parallel to the bend line. Specifically, the CNC brake operator pushes the edge of the part into a back gauge to ensure that the depth and angle of the bend is correct. The two sloped sides required me to modify their flanges. Fortunately, SolidWorks has a specific feature which makes that easy. The recessed box required five corner bend reliefs. These parts required me to learn a few new sheet metal tricks. 7 heat/vibration isolators (purple parts)Ī fair amount of welding (green pieces to the gray piece
